蘇州科舵許宏:“雙碳”目標的背后,需要工業(yè)互聯(lián)網的一份力
百萬年來,人類從起源、演化到文明社會的發(fā)展,一直都離不開與自然的共生與共處,所以生態(tài)環(huán)境的問題,也自古有之?鬃诱f,“子釣而不綱,弋不射宿”,說的是不可濫捕濫殺;荀子也說,“斬伐養(yǎng)長,不失其時”,講的是樹木養(yǎng)伐之道。一言蔽之,就是人與自然的相處應一切有度。
“有度”意味著平衡,意味著有張即有馳、有加即有減。所以,當工業(yè)文明發(fā)展帶來了污染物的過度排放之后,生態(tài)的問題最終也必須靠減排來解決。
去年,我國向全球做出“2030年前碳達峰、2060年前碳中和”的承諾,表明我國在生態(tài)文明建設方面的決心和目標。而要實現這個目標,需要每一個人、每一個團體學會“做減法”,少用一張紙、少開一天車,對于生產企業(yè)而言,不但要考慮增效降本,更要考慮如何滿足更高要求的節(jié)能減排標準。
通常來說,企業(yè)會從幾個方面著手實現節(jié)能減排,包括采用更先進的工藝和設備、降低動力能耗、加強能源的管理等等,F如今,加上大數據、云計算、5G、人工智能等數字化技術的應用,所有這些環(huán)節(jié)還能被進一步優(yōu)化和完善。比如,通過對生產全過程的實時狀態(tài)進行感知、監(jiān)測和數據收集,然后經過算法模型的分析,就能夠實現對各類資源的動態(tài)整合和有效控制;再比如,將節(jié)能相關的流程、過程參數、算法融合進工藝設計,根據實際生產場景,生成最優(yōu)的模型組合,在提高單體設備生產效率的同時,還可以降低能量消耗,從源頭上實現節(jié)能。
數字化技術助力企業(yè)減排與降本
作為環(huán)保和制藥設備的工程設計和制造企業(yè),蘇州科舵工程技術有限公司(以下簡稱“蘇州科舵”)正在很好地把這些技術融入到設備的工藝設計中。
據蘇州科舵數智工業(yè)部總監(jiān)兼首席信息官許宏向至頂網記者介紹,蘇州科舵的核心產品覆蓋了各個方面,包括藥企在原藥生產過程中所需的固液體分離技術、不同液體混合物的分離技術,以及三廢處理過程中對污染氣體、液體和固態(tài)顆粒物的有機處理技術等等。“現在,我們正在努力在所有這一系列產品中附加上數字化能力。”
蘇州科舵數智工業(yè)部總監(jiān)兼首席信息官 許宏
其中,比較常規(guī)的做法之一,就是在生產性設備端實現數據采集和數據分析,通過對設備運行狀況的監(jiān)測和識別,達到預測性維護、備品備件管理和資源預測性調撥,這不但能提高設備的生產效率,還能減少在生產過程中的非計劃停機,從而達到“節(jié)能減排”的目的。
不過,要滿足環(huán)保的要求,更重要的還要做好三廢處理。在生產企業(yè),一般會通過活性炭吸附技術,在廢氣和廢水處理過程中吸附有害物質,比如去除污水濃縮過程產生的膠粘物質,從而提升濃縮設備的傳熱性能,間接達到節(jié)能減排的效果,同時也保護設備的正常運行,降低設備維護成本。
這個過程如果引入數字化技術,不僅可以幫助企業(yè)更好地滿足環(huán)保規(guī)范,還能夠從各個方面減少成本浪費。“舉例來說,基于數字化分析,它就會告訴我們,活性炭的吸附率呈現什么樣的趨勢,從而幫助企業(yè)決定是否增加或者替換活性炭輔料。”許宏解釋說,“以前企業(yè)往往要靠經驗,經常需要多備庫存,這不僅會產生庫存成本,另外由于活性炭的保存對環(huán)境有比較高的要求,所以也會產生自然損耗。而有了數據預測模型之后,就可以對活性炭這種高附加值的輔料和催化劑進行動態(tài)調節(jié)。”
并且,這樣的動態(tài)調節(jié)還可以延伸到供應鏈端。“比如說,模型預測在3天后需要采購10噸活性炭,加上物流時間,采購部門就可以很快得到向供應商下單的時間,從而優(yōu)化物料庫存量和財務現金流。”許宏表示。
工業(yè)互聯(lián)網平臺賦能產業(yè)協(xié)同
據了解,目前蘇州科舵已經把大量的預測模型算法組合融入到設備工程的各個關鍵節(jié)點,不斷地優(yōu)化工藝流程。而許宏認為,未來基于工業(yè)互聯(lián)生態(tài)平臺的構建,數字化技術所能帶來的價值,還會輻射至整個產業(yè),推動產業(yè)鏈之間的協(xié)同和“雙碳”目標的實現。
許宏強調,工業(yè)互聯(lián)網不應該是某個企業(yè)的平臺,而是“公共”的生態(tài)性平臺,“也就是說,產業(yè)鏈上不同的利益相關方都可以把自己的產品放到同一個平臺上,并且從平臺上獲取相應的信息,然后通過數字技術分析去指導企業(yè)業(yè)務的發(fā)展。”
還以上述的活性炭輔料的采購為例。當某生產企業(yè)與其供應商把相關信息都共享在同一工業(yè)互聯(lián)網平臺之上,生產企業(yè)在輔料即將用完之前,供應商就可以基于數據預測提前備出對應的采購量,并按照預期時間安排發(fā)貨,如此一來,就能減少中間的多次溝通、下單等繁瑣操作,真正做到上下游的有效協(xié)同。相反地,生產企業(yè)在掌握上游供應商供貨情況的前提下,也可以更靈活地管理自己的供應鏈體系,更好地安排生產進度。
另一方面,針對“雙碳”目標的實現,工業(yè)互聯(lián)網也被認為可以發(fā)揮很大的作用。舉例來說,過去,相關數據互不相通、信息孤島的存在是導致生態(tài)環(huán)境管控難的一大問題。而基于工業(yè)互聯(lián)網,就可以構建一個區(qū)域信息共享數據庫,把相關的機構、部門和企業(yè)納入進來,并借助平臺之上的大數據、人工智能等技術,實現對該區(qū)域生態(tài)環(huán)境、資源消耗情況和碳排放狀況的實時監(jiān)測和協(xié)同治理。
在挑戰(zhàn)與變化中摸索前行
總而言之,技術的價值將在各個領域被釋放,滿足企業(yè)生產的各種需求,而企業(yè)的唯一選項就是去“擁抱”它。
比如,在生產制造過程中,有很多的經驗化標準都可以抽取出來,以人工智能算法模型的方式放到設備的工藝設計中,或者構建在工業(yè)互聯(lián)網平臺之上,而人在其中的作用,主要就是輸入數據,然后根據輸出的數據進行分析和決策。也就是說,人工智能可以在很多場景幫人“打輔助”。
當然,隨著數據量的大幅增加和人工智能的深入應用,這對企業(yè)IT基礎設施設施的計算能力也會提出更高的要求,比如在一些本地模型訓練的場景,甚至需要用到GPU服務器。而在機械制造業(yè),除了生產端,針對圖形的并行計算,GPU的需求也是比較大的。“它可以幫助研發(fā)設計人員實現在線協(xié)同設計和統(tǒng)一數據管理,并且設計模型數據量越大、設計人員越多,企業(yè)的數據中心就越要往這方向做部署。”許宏表示。
不過,在他看來,能用技術解決的都還不是最大的問題,在企業(yè)進行數字化轉型、引入新技術的過程中,企業(yè)業(yè)務模式、運營方式和工藝流程的創(chuàng)新才是最大的挑戰(zhàn)。
“其中的關鍵在于,企業(yè)能不能快速轉變成一個創(chuàng)新型的柔性組織,快速地在資源調配和組織關系等方面做出調整。”出于這樣的理念,現如今的蘇州科舵正在積極地融入這樣的變化,而他個人,也正在直面其中的挑戰(zhàn),不斷摸索前行。
本文章選自《數字化轉型方略》雜志,閱讀更多雜志內容,請掃描下方二維碼
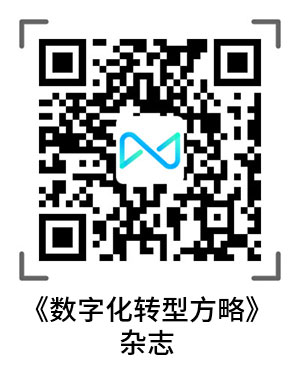