基于5G+AR的大型船企云制造平臺(tái)
構(gòu)建全壽命周期數(shù)字造船新模式,促進(jìn)船舶行業(yè)變革
長期以來,船舶工業(yè)是重工行業(yè),生產(chǎn)制造條件艱苦,數(shù)字化、智能化生產(chǎn)轉(zhuǎn)型始終面臨許多客觀限制與技術(shù)障礙。新一代ICT技術(shù)在船舶建造領(lǐng)域的應(yīng)用面相對(duì)狹窄,對(duì)船舶建造全流程的整體效率和質(zhì)量提升效果不夠顯著。
針對(duì)深遠(yuǎn)海“雙高”(高技術(shù)、高附加值)船舶裝備平臺(tái)大型化、新研裝置多且系統(tǒng)復(fù)雜、性能要求高、成本控制嚴(yán)及高度個(gè)性化定制等顯著特點(diǎn),中國船舶下屬江南造船等企業(yè)打造基于5G+AR的云制造平臺(tái),集成總裝廠-供應(yīng)商、研發(fā)設(shè)計(jì)-制造現(xiàn)場、制造-檢驗(yàn)的多層次多維度協(xié)同關(guān)系,打通研發(fā)設(shè)計(jì)-供應(yīng) -制造-檢驗(yàn)的云協(xié)同流程,構(gòu)建適用于船舶行業(yè)的全壽命周期數(shù)字造船新模式。
基于5G+AR的云制造平臺(tái)應(yīng)用場景豐富
基于5G+AR的大型船企云制造平臺(tái)主要由基礎(chǔ)設(shè)施層、硬件設(shè)備層、軟件平臺(tái)層、內(nèi)部協(xié)同層及應(yīng)用層組成。其中基礎(chǔ)設(shè)施層由互聯(lián)網(wǎng)和江南私有云組成;硬件設(shè)備層主要包括涉及的相關(guān)硬件設(shè)備,如服務(wù)器、AR眼鏡等;軟件平臺(tái)層則包括了設(shè)計(jì)軟件、協(xié)同平臺(tái)等,內(nèi)部協(xié)同層展示了平臺(tái)內(nèi)部各版塊間的協(xié)同關(guān)系,應(yīng)用層則由平臺(tái)對(duì)應(yīng)的應(yīng)用場景組成,其技術(shù)架構(gòu)如下圖所示。
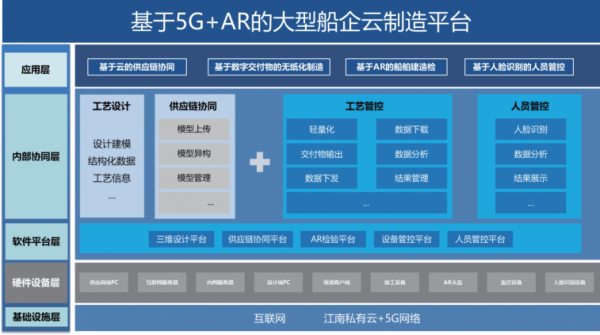
有別于單一數(shù)字模型的數(shù)字化轉(zhuǎn)型,本案例運(yùn)用供應(yīng)鏈云協(xié)同與模型轉(zhuǎn)化、基于MBD的制造交付物生成、基于AR的船舶建造檢驗(yàn)技術(shù)等技術(shù),覆蓋協(xié)同設(shè)計(jì)、無紙化建造、AR檢驗(yàn)、車間數(shù)字化管控等業(yè)務(wù)場景,形成了包括基于云的供應(yīng)鏈協(xié)同、基于數(shù)字交付物的無紙化制造、基于AR的船舶建造檢驗(yàn)以及基于人臉識(shí)別的人員管控等功能,通過數(shù)字化手段對(duì)船舶制造過程實(shí)施精準(zhǔn)管控。
基于5G+AR的云制造平臺(tái)應(yīng)用價(jià)值顯著
基于5G+AR的云制造平臺(tái)上線應(yīng)用后,打破企業(yè)間及部門間的溝通壁壘,減少設(shè)計(jì)及制造環(huán)節(jié)的信息模態(tài)轉(zhuǎn)換,實(shí)現(xiàn)多端模型-數(shù)據(jù)-業(yè)務(wù)的云上協(xié)同,有效減少設(shè)計(jì)員、工人等的重復(fù)性低價(jià)值勞動(dòng),在設(shè)計(jì)效率、制造效率、檢驗(yàn)效率、生產(chǎn)人員管控效率提升等方面的提升效果顯著,可降低企業(yè)用工成本約3億/年。
1.基于云的供應(yīng)鏈協(xié)同方面,液化氣船、大型集裝箱船、高新產(chǎn)品等船型全面應(yīng)用,單船平均上傳設(shè)備模型350余項(xiàng),設(shè)備建模效率和質(zhì)量有效提高,設(shè)計(jì)成本節(jié)約120萬/年。
2.基于模型的無紙化建造方面,液化氣船、集裝箱船等20余型船舶產(chǎn)品全面應(yīng)用,可縮短船舶建造周期、提高建造質(zhì)量,以每年交付20艘計(jì)算,可降低建造成本約1億/年。
3.基于AR的船舶建造檢驗(yàn)方面,液化氣船、集裝箱船等關(guān)鍵建造環(huán)節(jié)等全面應(yīng)用,檢驗(yàn)效率提升平均達(dá)到50%以上,可降低人工成本約200萬/年。
4.基于人臉的車間管控方面,精細(xì)化派工報(bào)工管理實(shí)現(xiàn)工人生產(chǎn)效率平均提升10%,公司2萬工人可降低人工成本2億/年。
中國船舶下屬江南造船等企業(yè)首次在船舶行業(yè)提出、構(gòu)建并應(yīng)用了的基于5G+AR的云制造平臺(tái),相較于傳統(tǒng)造船模式實(shí)現(xiàn)了質(zhì)量和效率的變革式提升,在實(shí)現(xiàn)產(chǎn)業(yè)鏈上下游互聯(lián)互通的同時(shí),縮短了企業(yè)內(nèi)外部信息傳遞和共享、技術(shù)交流和溝通時(shí)間,打造了總裝廠-供應(yīng)商、研發(fā)設(shè)計(jì)-制造現(xiàn)場、制造-檢驗(yàn)的協(xié)同、共享、共贏新模式。
同時(shí),平臺(tái)建設(shè)成果得到省部級(jí)領(lǐng)導(dǎo)、船舶、海工、航空、建筑、能源以及工業(yè)軟件等企業(yè)500余次的考察與交流,有效促進(jìn)了行業(yè)內(nèi)外整體數(shù)字化轉(zhuǎn)型與發(fā)展。
本文章選自中國上市公司協(xié)會(huì)發(fā)布的《中國上市公司數(shù)字化轉(zhuǎn)型典型案例》